6 Key Cost Components of the Order Fulfilment Process
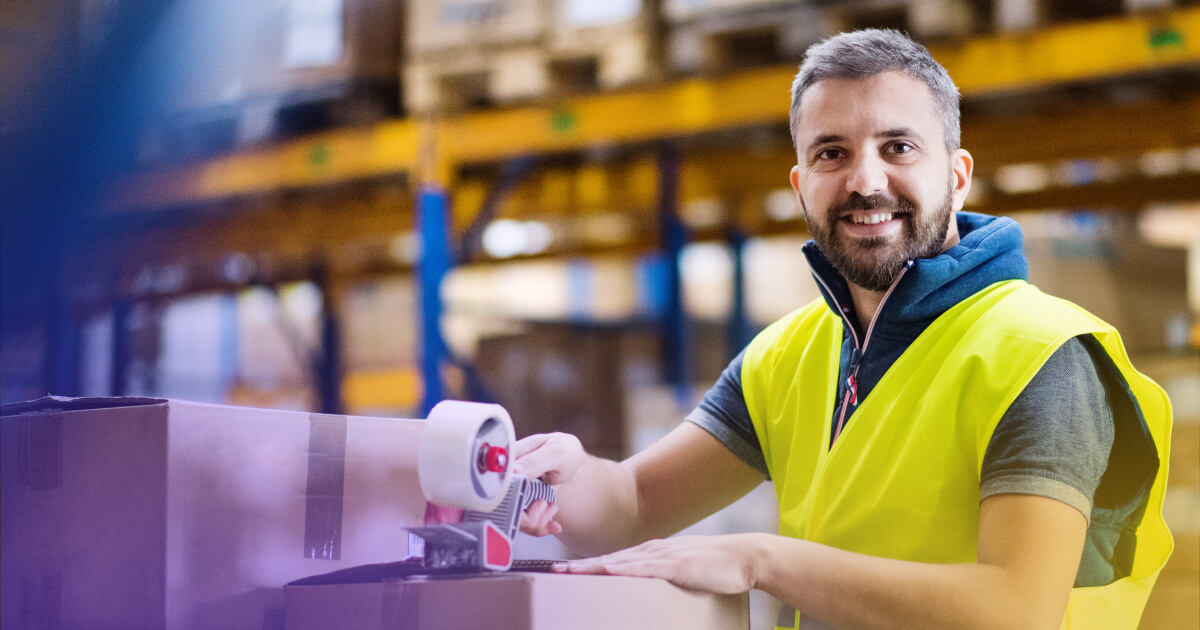
Understanding the cost components of the order fulfilment process is essential for businesses aiming to optimise their operations and increase profitability. Each stage of the fulfilment process incurs specific costs that can be managed and reduced with the right strategies.
In this article, we’ll explore six key components of order fulfilment costs, strategies to minimise expenses related to all aspects of order fulfilment and how Codept can help businesses achieve this.
Key Cost Components
Understanding the detailed breakdown of warehousing, transportation, packaging, technology, returns management, and labour costs is crucial for effectively managing and reducing overall fulfilment expenses.
Let’s dig into those aspects in more detail…
1. Warehousing Costs
Warehousing costs are a significant part of the fulfilment process, encompassing various expenses related to the storage and handling of inventory.
Storage Fees
Storage fees are charges for storing inventory, typically based on space usage, such as per pallet or cubic metre. These fees can vary significantly depending on the warehouse location and the amount of space utilised. It’s important that businesses compare costs for storage fees and strategically choose the best option for them in order to minimise order fulfilment expenses.
Handling Fees
Handling fees are costs associated with receiving, storing, and picking goods. These include labour costs for warehouse workers who manage the physical movement of products within the warehouse.
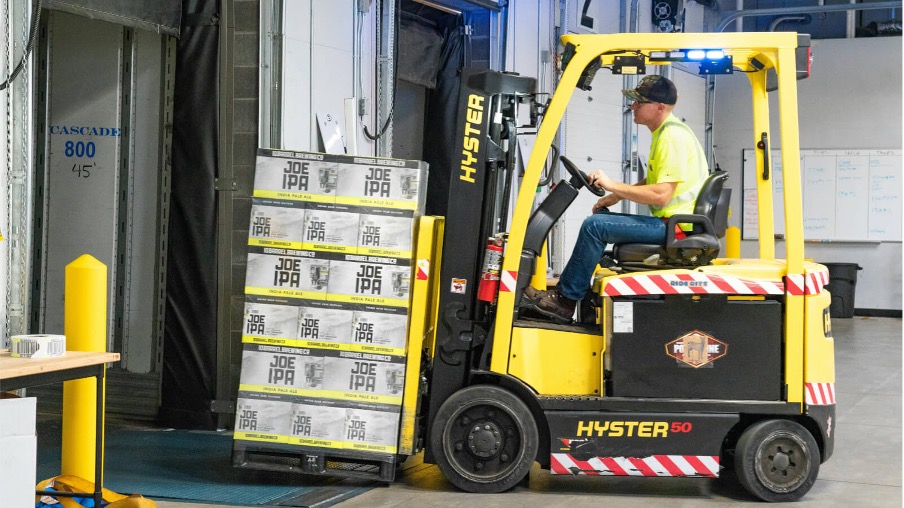
Efficient warehousing practices, such as optimising storage layouts and investing in warehouse management systems (WMS), can help reduce these costs by improving space utilisation and operational efficiency.
2. Transportation Costs
Transportation costs are incurred when moving goods from the warehouse to the customer, and they can significantly impact the overall fulfilment cost.
Shipping Fees
Shipping fees are expenses related to transporting goods to customers, influenced by factors such as volume, delivery speed and domestic or international shipping destinations.
Last-Mile Delivery
The last mile is often the most expensive segment, involving delivery to the customer's doorstep, with expenses related to transporting goods to customers influenced by factors such as distance, weight, and accessibility.
The last-mile delivery, which involves delivering the product to the customer's doorstep, is often the most expensive segment due to its resource requirements.
To mitigate these costs, businesses can negotiate better rates with carriers, based on volume and speed, and consolidate shipments to maximise efficiency. Leveraging regional distribution centres can also reduce last-mile delivery expenses by positioning inventory closer to end customers.
3. Packaging Costs
Packaging costs involve the materials and labour required to prepare products for shipment, ensuring they reach customers in good condition.
Material Costs
Choosing the right packaging materials is crucial for balancing cost and product protection. Expenses for boxes, tapes, labels, and protective materials like bubble wrap and foam peanuts can form a significant portion of order fulfilment costs.
It’s important to note that using sustainable packaging materials can potentially reduce costs through recycling programs, whilst also appealing to environmentally conscious consumers. A potential win-win scenario.
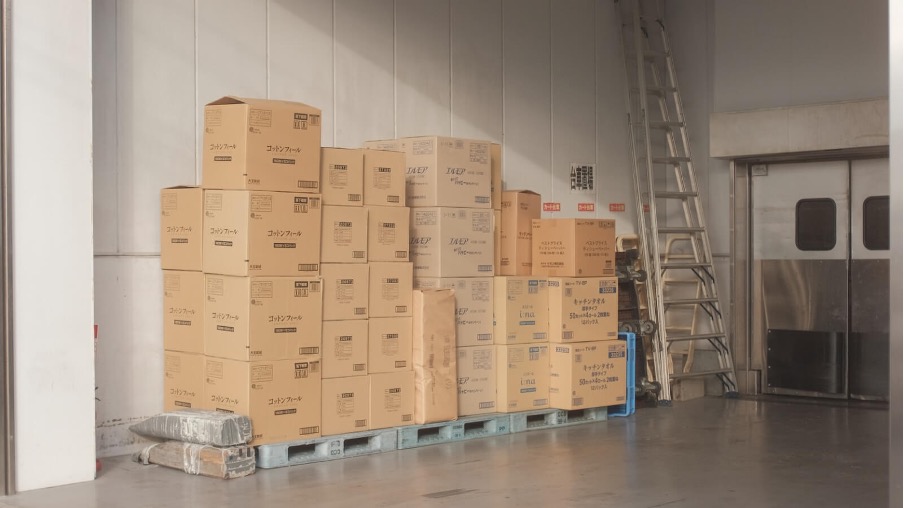
Labour Costs
Labour costs in packaging are associated with the time and effort spent on packing orders. Since this is often based on human labour, the costs here can be a high portion of total order fulfilment expense. However, there are ways to reduce this:
- Staff Efficiency: With efficient packing processes and employee training, productivity can be increased, reducing expenses in proportion. Additionally, storing products in a way so that picking times are optimised by demand also boosts productivity.
- Leveraging AI and robotics: Implementing automated packing solutions can significantly reduce packaging costs by increasing speed, accuracy and operational uptime, all whilst minimising material waste.
4. Technology Costs
Investing in technology is crucial for modern fulfilment operations, providing tools to enhance efficiency, accuracy, and scalability. Technology costs come two-fold:
Order Fulfilment Software
Software investments include fulfilment management systems and warehouse management systems (WMS) that streamline operations, reduce errors, and improve overall efficiency can incur expensive recurring costs, especially when charged per staff member or by volume.
According to Explore WMS, businesses should “expect to pay at least $100 per user for entry-level services that have a basic level of functionality.”
- Basic WMS Software: $100 per user per month (entry-level services that have a basic level of functionality)
- Mid-Term WMS Software: $200-300 per user per month (more functionality, such as fleet management tools or analytics designed to increase picking efficiency)
- Enterprise WMS Software: $500+ per user per month (include advanced functionality, such as tools that help you create a sophisticated audit trail or maintain industry compliance)
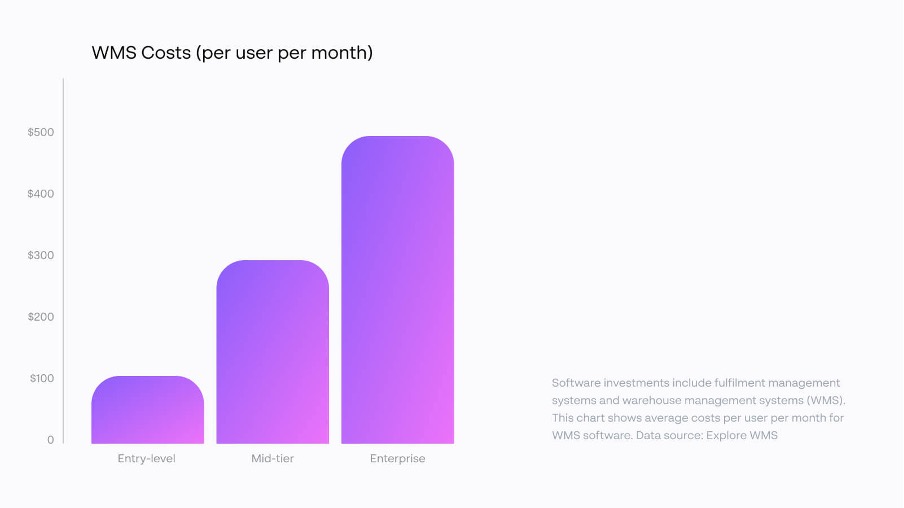
Middleware Providers
Alongside a warehouse management system, many companies face additional charges for middleware providers - a company or platform that acts as an intermediary between different systems, such as ecommerce platforms, warehouse management systems (WMS), shipping carriers, and other logistics software.
Whilst middleware providers streamline communication and ensure that data flows seamlessly across various systems, they can become extremely costly, and often present challenges or limitations as they look to integrate with multiple platforms.
Using the Codept platform, on the other hand, removes the need for having experts handling complex middleware software and tasks such as mapping, configuration and deployments. Each new merchant integration usually requires hours of work and project coordination covered through limited consultancy resources, while our solution can be handled by anyone, regardless of their previous IT know-how. Codept also gives you direct access to an “integration on demand” team that will assist you with any project or technical needs.
ERP Software
ERP (Enterprise Resource Planning) software is yet another expense faced by businesses to manage and integrate key business processes in a unified system.
An ERP has its advantages in allowing businesses to centralise data from various departments, typically covering a wide range of functions, however, the costs quickly stack up for enterprise solutions like SAP, Oracle NetSuite, and Microsoft Dynamics.
Hardware
Hardware costs cover necessary equipment like barcode scanners, computers, and printers. Whilst advanced hardware can improve the speed and accuracy of various fulfilment tasks, it is not cheap to set up initially, requiring a large amount of capital.
The return on investment (ROI) for technology can be substantial, with improved inventory management, faster processing times, and enhanced customer satisfaction. Businesses should regularly evaluate their technology stack to ensure it aligns with operational goals and adapts to changing market demands.
5. Returns Management Costs
Often overlooked, managing returns efficiently is a crucial aspect of the order fulfilment process, impacting customer satisfaction and overall costs.
Processing returns involves expenses related to handling returned products, such as transportation back to the warehouse, inspection, restocking, and potential refurbishment or disposal of damaged items.
Streamlining the returns process with clear policies and efficient systems can reduce costs and improve customer loyalty. Implementing automated return authorisation systems and using analytics to identify patterns can help mitigate return rates and associated costs.
6. Labour Costs
Labour costs are a significant component of order fulfilment expenses, encompassing wages for employees involved in various stages of the process.
Staffing costs can include wages for warehouse workers, supervisors, customer service representatives and delivery drivers, to name just a few important roles along the order fulfilment process.
According to Erieri, in 2024, the average hourly rate for a warehouse worker in Germany is approximately €18 per hour. With this in mind, just one full-time member would cost €37,964 per year, and this is expected to rise by 15% until 2029.
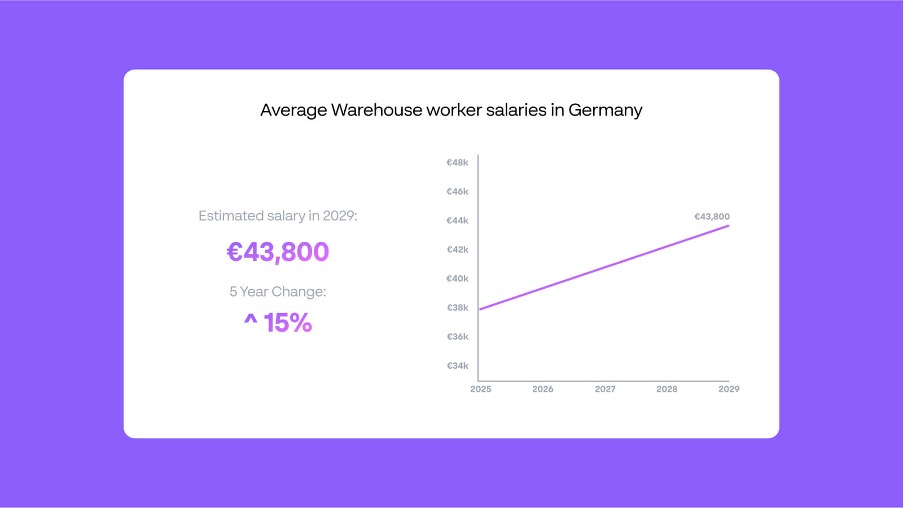
Labour costs can fluctuate based on the volume of orders and seasonal demand, so optimising the costs involves balancing workforce levels with demand and providing training to improve productivity.
With advancements in technology, automation, AI, robotics and machine learning can also reduce reliance on manual labour, leading to cost savings.
How to Calculate Order Fulfilment Costs
Calculating order fulfilment costs involves a comprehensive analysis of all expenses incurred during the process.
Here's a step-by-step guide:
Identify All Relevant Order Fulfilment Costs
- Fixed Costs: These include warehouse rent, utilities, and technology investments. These costs remain constant regardless of the volume of orders processed.
- Variable Costs: These vary with the volume of orders and include shipping, packaging, and labour. As order volume grows, these costs increase proportionally.
Calculate Per-Order Costs
- Storage Costs: Determine the cost of storage per unit of inventory (e.g., per pallet per day). Multiply by the average inventory levels to get the total storage cost.
- Handling Costs: Calculate the cost per pick and pack operation. This includes labour costs and any equipment usage.
- Shipping Costs: Calculate these by determining the average shipping cost per order, considering different shipping zones and methods.
Consider Additional Costs
- Returns: Estimate the cost of processing returns, including transportation back to the warehouse, inspection, and restocking.
- Packaging: Calculate the costs of packaging materials and the labour involved in packing.
Sum Up Total Order Costs
Add up all identified costs to get the total fulfilment cost then divide this total by the number of orders processed to get the average fulfilment cost per order.
For example, if the total monthly fulfilment costs amount to $50,000 and the business processes 10,000 orders in that month, the average fulfilment cost per order would be $5.
This calculation helps businesses understand their cost structure and identify areas for improvement.
How to Improve Fulfilment Performance to Increase Profitability
So how do you improve fulfilment performance? It’s critical for increasing operational efficiency and profitability, and the solution is multifaceted.
Here are some of our top strategies:
Streamline Processes
Automation can significantly enhance fulfilment performance by reducing errors and speeding up operations.
Implementing automated systems for tasks like picking, packing, and inventory management can streamline operations and reduce labour costs, whilst automated storage and retrieval systems (AS/RS), conveyor belts, and robotics can further enhance productivity and reduce order fulfilment costs.
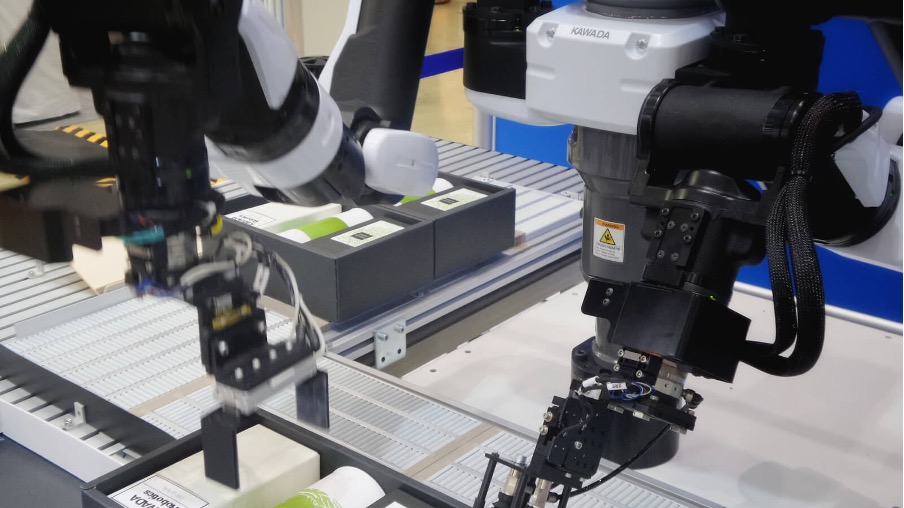
Integration of various systems using platforms like Codept simplifies the data flow between different software, improves accuracy through real-time data synchronisation, and reduces manual intervention by eliminating redundant tasks and minimising error-prone operations.
Seamless integration between order management, inventory management, and shipping systems ensures real-time visibility and coordination.
Optimise Inventory Management
Accurate demand forecasting is crucial for reducing overstock and stockouts, minimising unnecessary storage costs. Advanced forecasting tools use historical data, market trends, and AI to predict demand more accurately. This can reduce order fulfilment costs by reducing expenses for unnecessary stock and storage space.
What’s more, Just-in-Time (JIT) inventory practices reduce inventory holding times, decreasing storage fees and obsolescence risks.
Implementing a robust inventory management system can provide real-time visibility into stock levels, improve order accuracy, and reduce carrying costs. Regular inventory audits and cycle counting can also ensure inventory accuracy and prevent stock discrepancies.
Enhance Transportation Efficiency
Moving goods between warehouses and delivering to customers’ doorsteps takes a significant portion of the order fulfilment budget for any business; vehicles, drivers and fuel costs all add up.
For this reason, it’s important to reduce expenses where possible in order to minimise order fulfilment costs.
- Utilising software to plan the most efficient delivery routes can reduce travel distances, fuel consumption, and delivery times. Route optimisation tools consider factors like traffic, weather, and delivery windows to create optimal routes.
- Choosing the right mix of carriers based on cost, speed, and reliability can also optimise shipping expenses.
- Negotiating volume discounts with carriers and leveraging regional carriers for specific routes can provide cost savings. Implementing a transportation management system (TMS) can streamline carrier selection, track shipments in real-time, and provide analytics to identify cost-saving opportunities.
- Collaborative logistics, such as sharing transportation resources with other businesses, can also reduce costs.
Leverage 3PL Services
Third-party logistics (3PL) providers offer economies of scale and specialised expertise, reducing overall fulfilment costs.
Since 3PLs have established networks and infrastructure that can lower transportation and warehousing expenses and can provide flexibility in managing peak seasons and unexpected demand surges, businesses can scale operations up or down without significant investments in infrastructure.
Evaluating 3PL performance through regular audits and performance metrics can ensure service quality and cost-effectiveness, as well as establishing clear communication channels and collaborative partnerships with 3PL providers to further enhance fulfilment performance.
Using Codept to Increase Profitability & Streamline Order Fulfilment
Codept’s platform enhances fulfilment performance by providing seamless integration between e-tailers and logistics providers. This integration reduces the complexity and cost of managing multiple systems, allowing businesses to:
- Reduce Onboarding Time: Quick integration with new fulfilment partners accelerates time-to-market, enabling businesses to respond swiftly to market opportunities and customer demands. With our self-onboarding feature, businesses can autonomously connect merchants to their WMS system in just a matter of minutes, reducing the time to revenue generation. Cost-savings here can be significant as we eliminate the need for expensive consultancy services and integrations between multiple platforms.
- Improve Data Accuracy: Consistent and reliable data exchange minimises errors and operational disruptions, ensuring accurate and timely fulfilment. For merchants, this keeps costs low as they reduce the need to manually check data entries or waste resources correcting errors.
- Enhance Scalability: Easily scale operations with new partners and locations without significant IT overhead. Codept’s flexible platform supports business growth by accommodating increasing order volumes and expanding fulfilment networks. Unlike other solutions, once set up, you can add new partners with the click of the button, saving time and money spent on developer costs and intermediary software.
By focusing on key cost components and by leveraging our solution, businesses can significantly improve their fulfilment processes, enhance performance, and increase profitability.
Ready to transform order fulfilment?
Improve operational efficiency, streamline order fulfilment and scale your business profitably with Codept.
If you’re ready to shake up your technology solution, book a demo with us.
FAQs
What are the key components of fulfilment costs?
Fulfilment costs include warehousing fees, transportation expenses, packaging costs, technology investments, returns management costs, and labour charges.
How can a logistics provider reduce warehousing costs?
Reducing warehousing costs can be achieved through space optimisation, implementing efficient storage systems, and leveraging technology for better logistics management.
What is the role of a 3PL in fulfilment?
Third-party logistics (3PL) providers help manage and execute supply chain operations, offering cost savings, flexibility, and expertise in logistics and fulfilment.
How does technology impact fulfilment costs?
The initial investment in technology can be substantial but it pays for itself ten-fold by reducing errors, speeding up processes, and improving data accuracy. This ultimately lowers fulfilment costs long-term through automation and integration.
How can I improve fulfilment performance to increase profitability?
Improving fulfilment performance involves streamlining processes, optimising inventory management, enhancing transportation efficiency, and leveraging 3PL services.
What is last-mile delivery and why is it expensive?
Last-mile delivery is the final step of delivering a product to the customer. It is often expensive due to the complexity and resources required for door-to-door service.
How can Codept help in improving fulfilment performance?
Codept enhances fulfilment performance by providing seamless integration between e-tailers and logistics providers, reducing complexities and operational costs.
What are the common challenges in the fulfilment process?
Common challenges include managing inventory accurately, handling returns efficiently, and maintaining cost-effective transportation and storage solutions.
Why is demand forecasting important in fulfilment?
Accurate demand forecasting helps in reducing overstock and stockouts, optimising inventory levels, and minimising unnecessary storage and handling costs.
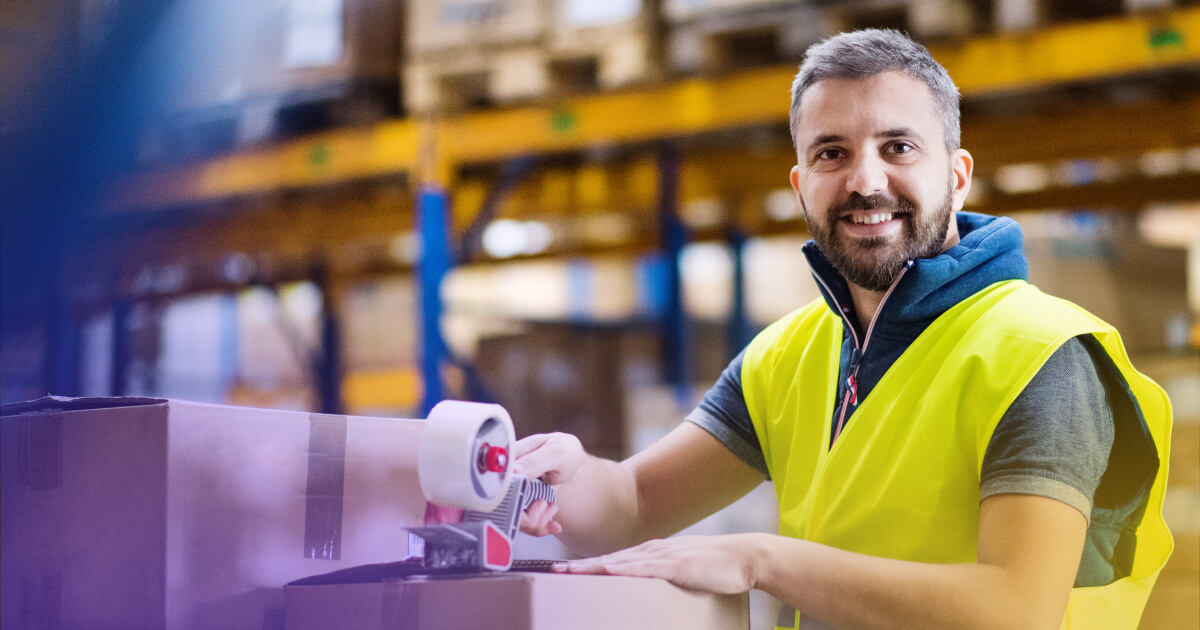
Understanding the cost components of the order fulfilment process is essential for businesses aiming to optimise their operations and increase profitability. Each stage of the fulfilment process incurs specific costs that can be managed and reduced with the right strategies.
In this article, we’ll explore six key components of order fulfilment costs, strategies to minimise expenses related to all aspects of order fulfilment and how Codept can help businesses achieve this.
Key Cost Components
Understanding the detailed breakdown of warehousing, transportation, packaging, technology, returns management, and labour costs is crucial for effectively managing and reducing overall fulfilment expenses.
Let’s dig into those aspects in more detail…
1. Warehousing Costs
Warehousing costs are a significant part of the fulfilment process, encompassing various expenses related to the storage and handling of inventory.
Storage Fees
Storage fees are charges for storing inventory, typically based on space usage, such as per pallet or cubic metre. These fees can vary significantly depending on the warehouse location and the amount of space utilised. It’s important that businesses compare costs for storage fees and strategically choose the best option for them in order to minimise order fulfilment expenses.
Handling Fees
Handling fees are costs associated with receiving, storing, and picking goods. These include labour costs for warehouse workers who manage the physical movement of products within the warehouse.
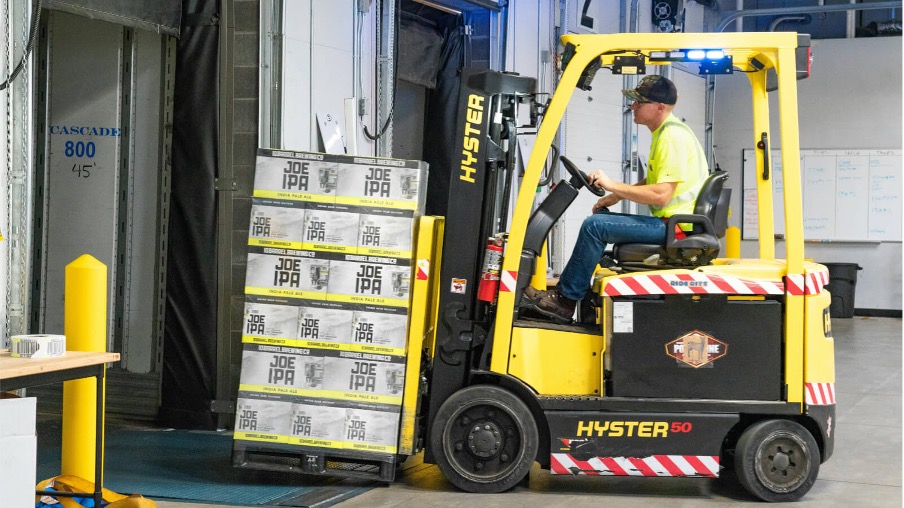
Efficient warehousing practices, such as optimising storage layouts and investing in warehouse management systems (WMS), can help reduce these costs by improving space utilisation and operational efficiency.
2. Transportation Costs
Transportation costs are incurred when moving goods from the warehouse to the customer, and they can significantly impact the overall fulfilment cost.
Shipping Fees
Shipping fees are expenses related to transporting goods to customers, influenced by factors such as volume, delivery speed and domestic or international shipping destinations.
Last-Mile Delivery
The last mile is often the most expensive segment, involving delivery to the customer's doorstep, with expenses related to transporting goods to customers influenced by factors such as distance, weight, and accessibility.
The last-mile delivery, which involves delivering the product to the customer's doorstep, is often the most expensive segment due to its resource requirements.
To mitigate these costs, businesses can negotiate better rates with carriers, based on volume and speed, and consolidate shipments to maximise efficiency. Leveraging regional distribution centres can also reduce last-mile delivery expenses by positioning inventory closer to end customers.
3. Packaging Costs
Packaging costs involve the materials and labour required to prepare products for shipment, ensuring they reach customers in good condition.
Material Costs
Choosing the right packaging materials is crucial for balancing cost and product protection. Expenses for boxes, tapes, labels, and protective materials like bubble wrap and foam peanuts can form a significant portion of order fulfilment costs.
It’s important to note that using sustainable packaging materials can potentially reduce costs through recycling programs, whilst also appealing to environmentally conscious consumers. A potential win-win scenario.
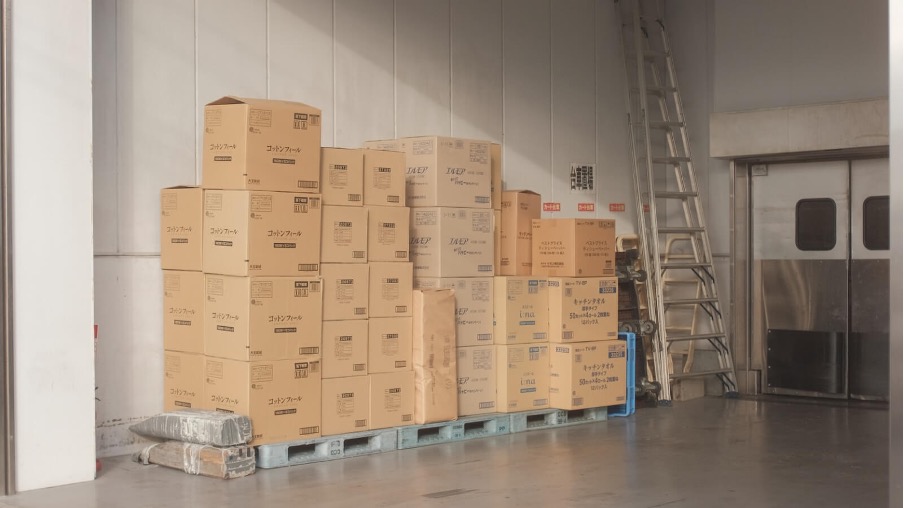
Labour Costs
Labour costs in packaging are associated with the time and effort spent on packing orders. Since this is often based on human labour, the costs here can be a high portion of total order fulfilment expense. However, there are ways to reduce this:
- Staff Efficiency: With efficient packing processes and employee training, productivity can be increased, reducing expenses in proportion. Additionally, storing products in a way so that picking times are optimised by demand also boosts productivity.
- Leveraging AI and robotics: Implementing automated packing solutions can significantly reduce packaging costs by increasing speed, accuracy and operational uptime, all whilst minimising material waste.
4. Technology Costs
Investing in technology is crucial for modern fulfilment operations, providing tools to enhance efficiency, accuracy, and scalability. Technology costs come two-fold:
Order Fulfilment Software
Software investments include fulfilment management systems and warehouse management systems (WMS) that streamline operations, reduce errors, and improve overall efficiency can incur expensive recurring costs, especially when charged per staff member or by volume.
According to Explore WMS, businesses should “expect to pay at least $100 per user for entry-level services that have a basic level of functionality.”
- Basic WMS Software: $100 per user per month (entry-level services that have a basic level of functionality)
- Mid-Term WMS Software: $200-300 per user per month (more functionality, such as fleet management tools or analytics designed to increase picking efficiency)
- Enterprise WMS Software: $500+ per user per month (include advanced functionality, such as tools that help you create a sophisticated audit trail or maintain industry compliance)
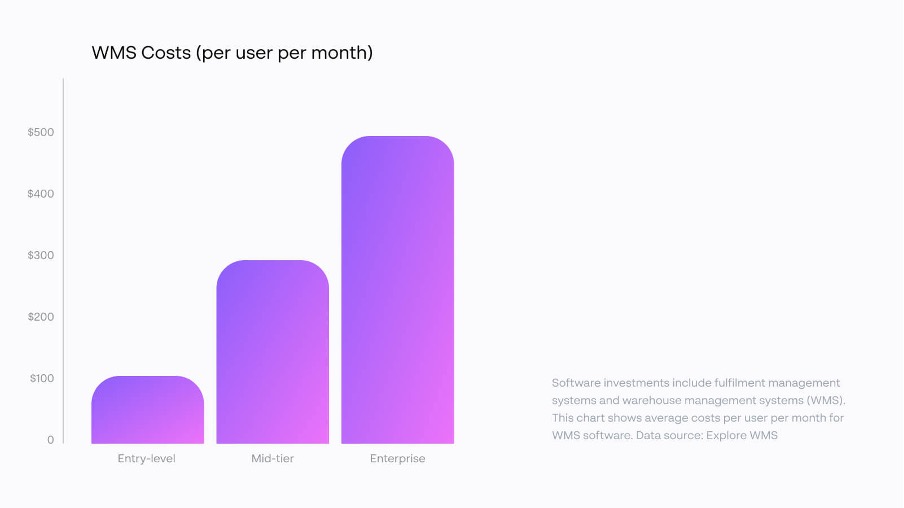
Middleware Providers
Alongside a warehouse management system, many companies face additional charges for middleware providers - a company or platform that acts as an intermediary between different systems, such as ecommerce platforms, warehouse management systems (WMS), shipping carriers, and other logistics software.
Whilst middleware providers streamline communication and ensure that data flows seamlessly across various systems, they can become extremely costly, and often present challenges or limitations as they look to integrate with multiple platforms.
Using the Codept platform, on the other hand, removes the need for having experts handling complex middleware software and tasks such as mapping, configuration and deployments. Each new merchant integration usually requires hours of work and project coordination covered through limited consultancy resources, while our solution can be handled by anyone, regardless of their previous IT know-how. Codept also gives you direct access to an “integration on demand” team that will assist you with any project or technical needs.
ERP Software
ERP (Enterprise Resource Planning) software is yet another expense faced by businesses to manage and integrate key business processes in a unified system.
An ERP has its advantages in allowing businesses to centralise data from various departments, typically covering a wide range of functions, however, the costs quickly stack up for enterprise solutions like SAP, Oracle NetSuite, and Microsoft Dynamics.
Hardware
Hardware costs cover necessary equipment like barcode scanners, computers, and printers. Whilst advanced hardware can improve the speed and accuracy of various fulfilment tasks, it is not cheap to set up initially, requiring a large amount of capital.
The return on investment (ROI) for technology can be substantial, with improved inventory management, faster processing times, and enhanced customer satisfaction. Businesses should regularly evaluate their technology stack to ensure it aligns with operational goals and adapts to changing market demands.
5. Returns Management Costs
Often overlooked, managing returns efficiently is a crucial aspect of the order fulfilment process, impacting customer satisfaction and overall costs.
Processing returns involves expenses related to handling returned products, such as transportation back to the warehouse, inspection, restocking, and potential refurbishment or disposal of damaged items.
Streamlining the returns process with clear policies and efficient systems can reduce costs and improve customer loyalty. Implementing automated return authorisation systems and using analytics to identify patterns can help mitigate return rates and associated costs.
6. Labour Costs
Labour costs are a significant component of order fulfilment expenses, encompassing wages for employees involved in various stages of the process.
Staffing costs can include wages for warehouse workers, supervisors, customer service representatives and delivery drivers, to name just a few important roles along the order fulfilment process.
According to Erieri, in 2024, the average hourly rate for a warehouse worker in Germany is approximately €18 per hour. With this in mind, just one full-time member would cost €37,964 per year, and this is expected to rise by 15% until 2029.
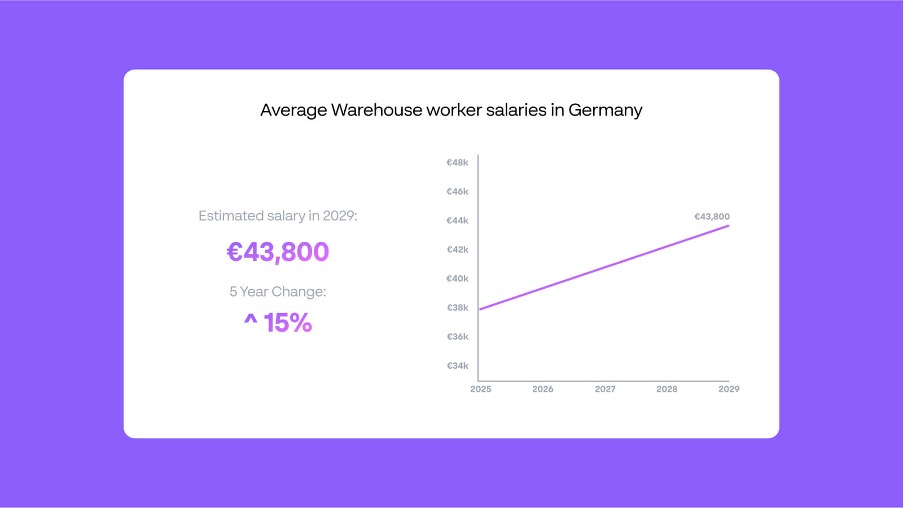
Labour costs can fluctuate based on the volume of orders and seasonal demand, so optimising the costs involves balancing workforce levels with demand and providing training to improve productivity.
With advancements in technology, automation, AI, robotics and machine learning can also reduce reliance on manual labour, leading to cost savings.
How to Calculate Order Fulfilment Costs
Calculating order fulfilment costs involves a comprehensive analysis of all expenses incurred during the process.
Here's a step-by-step guide:
Identify All Relevant Order Fulfilment Costs
- Fixed Costs: These include warehouse rent, utilities, and technology investments. These costs remain constant regardless of the volume of orders processed.
- Variable Costs: These vary with the volume of orders and include shipping, packaging, and labour. As order volume grows, these costs increase proportionally.
Calculate Per-Order Costs
- Storage Costs: Determine the cost of storage per unit of inventory (e.g., per pallet per day). Multiply by the average inventory levels to get the total storage cost.
- Handling Costs: Calculate the cost per pick and pack operation. This includes labour costs and any equipment usage.
- Shipping Costs: Calculate these by determining the average shipping cost per order, considering different shipping zones and methods.
Consider Additional Costs
- Returns: Estimate the cost of processing returns, including transportation back to the warehouse, inspection, and restocking.
- Packaging: Calculate the costs of packaging materials and the labour involved in packing.
Sum Up Total Order Costs
Add up all identified costs to get the total fulfilment cost then divide this total by the number of orders processed to get the average fulfilment cost per order.
For example, if the total monthly fulfilment costs amount to $50,000 and the business processes 10,000 orders in that month, the average fulfilment cost per order would be $5.
This calculation helps businesses understand their cost structure and identify areas for improvement.
How to Improve Fulfilment Performance to Increase Profitability
So how do you improve fulfilment performance? It’s critical for increasing operational efficiency and profitability, and the solution is multifaceted.
Here are some of our top strategies:
Streamline Processes
Automation can significantly enhance fulfilment performance by reducing errors and speeding up operations.
Implementing automated systems for tasks like picking, packing, and inventory management can streamline operations and reduce labour costs, whilst automated storage and retrieval systems (AS/RS), conveyor belts, and robotics can further enhance productivity and reduce order fulfilment costs.
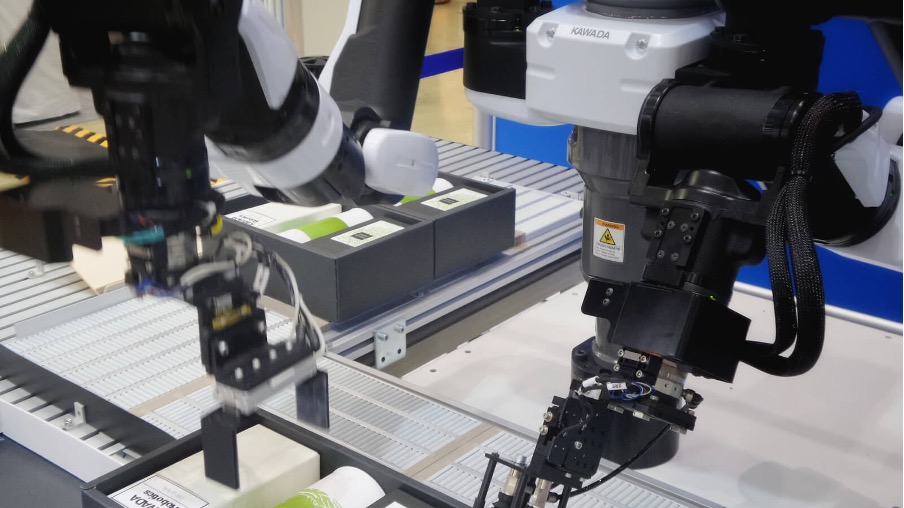
Integration of various systems using platforms like Codept simplifies the data flow between different software, improves accuracy through real-time data synchronisation, and reduces manual intervention by eliminating redundant tasks and minimising error-prone operations.
Seamless integration between order management, inventory management, and shipping systems ensures real-time visibility and coordination.
Optimise Inventory Management
Accurate demand forecasting is crucial for reducing overstock and stockouts, minimising unnecessary storage costs. Advanced forecasting tools use historical data, market trends, and AI to predict demand more accurately. This can reduce order fulfilment costs by reducing expenses for unnecessary stock and storage space.
What’s more, Just-in-Time (JIT) inventory practices reduce inventory holding times, decreasing storage fees and obsolescence risks.
Implementing a robust inventory management system can provide real-time visibility into stock levels, improve order accuracy, and reduce carrying costs. Regular inventory audits and cycle counting can also ensure inventory accuracy and prevent stock discrepancies.
Enhance Transportation Efficiency
Moving goods between warehouses and delivering to customers’ doorsteps takes a significant portion of the order fulfilment budget for any business; vehicles, drivers and fuel costs all add up.
For this reason, it’s important to reduce expenses where possible in order to minimise order fulfilment costs.
- Utilising software to plan the most efficient delivery routes can reduce travel distances, fuel consumption, and delivery times. Route optimisation tools consider factors like traffic, weather, and delivery windows to create optimal routes.
- Choosing the right mix of carriers based on cost, speed, and reliability can also optimise shipping expenses.
- Negotiating volume discounts with carriers and leveraging regional carriers for specific routes can provide cost savings. Implementing a transportation management system (TMS) can streamline carrier selection, track shipments in real-time, and provide analytics to identify cost-saving opportunities.
- Collaborative logistics, such as sharing transportation resources with other businesses, can also reduce costs.
Leverage 3PL Services
Third-party logistics (3PL) providers offer economies of scale and specialised expertise, reducing overall fulfilment costs.
Since 3PLs have established networks and infrastructure that can lower transportation and warehousing expenses and can provide flexibility in managing peak seasons and unexpected demand surges, businesses can scale operations up or down without significant investments in infrastructure.
Evaluating 3PL performance through regular audits and performance metrics can ensure service quality and cost-effectiveness, as well as establishing clear communication channels and collaborative partnerships with 3PL providers to further enhance fulfilment performance.
Using Codept to Increase Profitability & Streamline Order Fulfilment
Codept’s platform enhances fulfilment performance by providing seamless integration between e-tailers and logistics providers. This integration reduces the complexity and cost of managing multiple systems, allowing businesses to:
- Reduce Onboarding Time: Quick integration with new fulfilment partners accelerates time-to-market, enabling businesses to respond swiftly to market opportunities and customer demands. With our self-onboarding feature, businesses can autonomously connect merchants to their WMS system in just a matter of minutes, reducing the time to revenue generation. Cost-savings here can be significant as we eliminate the need for expensive consultancy services and integrations between multiple platforms.
- Improve Data Accuracy: Consistent and reliable data exchange minimises errors and operational disruptions, ensuring accurate and timely fulfilment. For merchants, this keeps costs low as they reduce the need to manually check data entries or waste resources correcting errors.
- Enhance Scalability: Easily scale operations with new partners and locations without significant IT overhead. Codept’s flexible platform supports business growth by accommodating increasing order volumes and expanding fulfilment networks. Unlike other solutions, once set up, you can add new partners with the click of the button, saving time and money spent on developer costs and intermediary software.
By focusing on key cost components and by leveraging our solution, businesses can significantly improve their fulfilment processes, enhance performance, and increase profitability.
Ready to transform order fulfilment?
Improve operational efficiency, streamline order fulfilment and scale your business profitably with Codept.
If you’re ready to shake up your technology solution, book a demo with us.
FAQs
What are the key components of fulfilment costs?
Fulfilment costs include warehousing fees, transportation expenses, packaging costs, technology investments, returns management costs, and labour charges.
How can a logistics provider reduce warehousing costs?
Reducing warehousing costs can be achieved through space optimisation, implementing efficient storage systems, and leveraging technology for better logistics management.
What is the role of a 3PL in fulfilment?
Third-party logistics (3PL) providers help manage and execute supply chain operations, offering cost savings, flexibility, and expertise in logistics and fulfilment.
How does technology impact fulfilment costs?
The initial investment in technology can be substantial but it pays for itself ten-fold by reducing errors, speeding up processes, and improving data accuracy. This ultimately lowers fulfilment costs long-term through automation and integration.
How can I improve fulfilment performance to increase profitability?
Improving fulfilment performance involves streamlining processes, optimising inventory management, enhancing transportation efficiency, and leveraging 3PL services.
What is last-mile delivery and why is it expensive?
Last-mile delivery is the final step of delivering a product to the customer. It is often expensive due to the complexity and resources required for door-to-door service.
How can Codept help in improving fulfilment performance?
Codept enhances fulfilment performance by providing seamless integration between e-tailers and logistics providers, reducing complexities and operational costs.
What are the common challenges in the fulfilment process?
Common challenges include managing inventory accurately, handling returns efficiently, and maintaining cost-effective transportation and storage solutions.
Why is demand forecasting important in fulfilment?
Accurate demand forecasting helps in reducing overstock and stockouts, optimising inventory levels, and minimising unnecessary storage and handling costs.